Common problems and solutions for the quality of extrudedpvc
栏目:news 发布时间:2021-09-28 08:51
Wuxi Jiahong Plastic Technology Co., Ltd. has nearly 30 years of R&D and production experience in rigid transparentpvc granules, pvc pellet production....
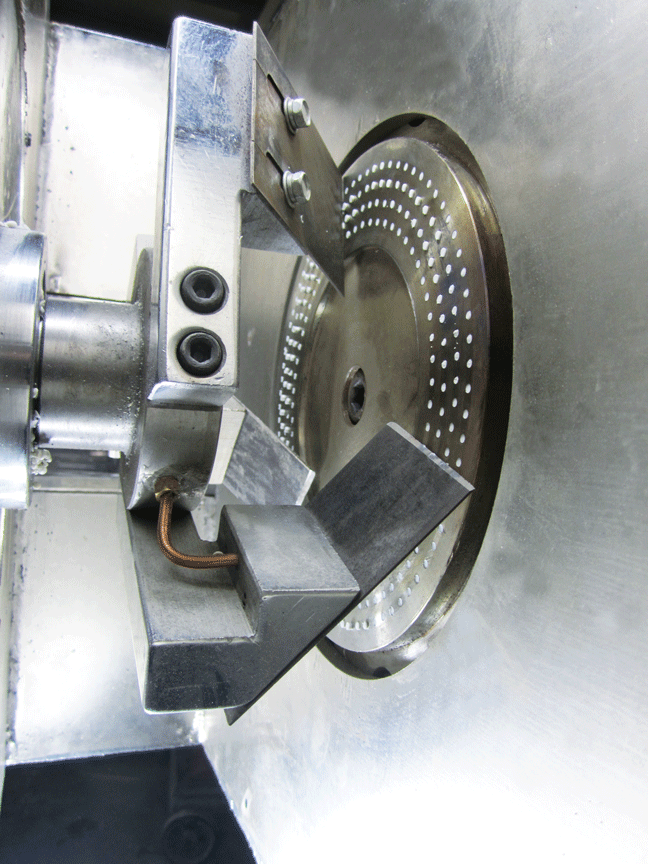
Extrudingpvc granules to pelletize is the most common mode of consumption for plastic manufacturers. The extruded particles sometimes exhibit certain problems in quality.
1. Long strip
Generally, lengths that are more than 2 times the normalpvc granules are regarded as long strips.
The main reasons for this are as follows: start-up or break, the direction of the material is not straight, the material is improperly immersed in water, the cutter of the pelletizer is worn or chipped, etc.
Main treatment measures:
1) During normal consumption, adjust the direction of the material strip entering the pelletizer and adjust the length of soaking water;
2) The squeezing process needs to be adjusted when the sliver is broken during consumption;
3) Pay attention to the inspection of the pelletizing mobile knife, and replace the damaged mobile knife in time;
4) Appropriate vibrating screens can be used to screen and dispose of the strips presented.
2. Connectpvc granules
Two or morepvc granules connected side by side are called continuous pellets.
The main reasons for the continuous granulation of the modified material are the failure to split or break the strip in time when driving the strip, the length of the water is not enough, and the temperature of the machine head is too high.
Main treatment measures:
1) When extruding the brace, select a nylon wheel with a suitable width for the guide strip, and separate the sticking strips in time;
2) Adjust the proper length of cooling water soaking, and even if the insulation strip is overheated, the continuous grain can be reduced;
3) Properly reduce the temperature of the machine head and adjust the temperature of the strip;
4) Regarding the present continuous granules, a vibrating sieve with appropriate mesh can be used for sieving.
3. Centipede
The cut surfaces of two or morepvc granules are not completely cut, and they are called centipede strips together, which actually belong to the category of connectingpvc granules.
The main reasons for this are the fast and slow speed when driving the strip, the feeding of the twin-screw extruder, the insufficient immersion length, the wear of the pelletizer cutter, or the excessively large gap between the fixed knife and the movable knife.
Main treatment measures:
1) The operator must pull the strip at a constant speed to prevent the strip from being too thick;
2) Adjust the appropriate squeezing process to prevent the material from coming out of the feed opening;
3) Adjust the appropriate cooling water immersion length to prevent the strip from overheating;
4) Adjust the gap between the fixed knife and the movable knife, and you cannot change to a new tool.
4. Black spots
There are black speckled particles on the outside or inside of the particles.
The main reasons for the black spots are: unclean screw pumping and driving; black spots in the raw materials; screw carbonization; environmental pollution; man-made introduction. ,
Main treatment measures:
1) In the process of changing the product, the screw is not cleared and cleaned, and the screw can be re-pulled; the clearing point: "three ports", the screen behind the filter and the large head;
2) Strengthen incoming material inspection, especially filled mineral powder or flame retardants are more likely to show black spots and impurities; for example, Z30S or T30S particles containing sawdust in the package, low-level filled mineral powder or flame retardants; these are all Cannot be used to consume modified plastics that require severe black spots;
3) Pay attention to controlling the temperature of the conditioning barrel and the residence time of the material in the barrel to avoid excessively high processing temperature; that is, the corresponding extrusion process should be designed according to the formula of each product.
4) Pay attention to the surrounding environmental sanitation and adhere to the humidity in the air, and it is necessary to do a good job of separation and protection measures between the products of different colors.
5) It is necessary to periodically stop liquidation of auxiliary equipment of extrusion equipment such as: sink, pelletizer, etc.;
6) Every time the screen is changed, the remaining material on the moving screen and the template must be cleared to avoid carbonization for too long;
7) Pay attention that the floor material strips are strictly prohibited from entering the pelletizer to avoid bringing dust;
8) Anti-plastic static electricity, static electricity is easy to attract dust.
5. Discoloration
It is manifested as a sudden change in the color of the product during the consumption process, showing obvious color difference.
The main reasons for the discoloration are uneven mixing or incorrect mixing; the cleaning machine is not clean; the temperature is too high; the shear is too strong; there are impurities in the mixed material.
Main treatment measures:
1) Strictly follow the mixing process to ensure the evenness and correctness of the mixing;
2) After the cleaning is completed, someone will check to ensure that the cleaning is clean;
3) Control the extrusion temperature to avoid too high temperature to cause toner synthesis;
4) Choose an appropriate screw combination to prevent too strong shear;
5) There must be no impurities in the back admixture.
6. Poor vacuum
There are two or more vacuum holes or foaming on the cut surface ofpvc granules.
The main reasons for the formation of poor vacuum are insufficient vacuum, bad vacuum system, poor sealing, and material return.
Main treatment measures:
1) Regularly check and maintain the vacuum pump and vacuum pressure gauge;
2) Timely liquidate vacuum tanks, vacuum chambers, and vacuum pipelines.
3) Properly control the flow of the circulating water of the vacuum pump;
4) Process the vacuum return material and ensure that the vacuum cover is sealed well.
7. Iron filings or other metal particles
There are iron filings or other metal particles on the surface or in the middle of the plasticpvc granules.
The main causes are screw wear, moving knife broken, iron filings or other metal particles in the raw material.
Main treatment measures:
1) Check whether the screw, movable knife, vibrating screen, etc. are damaged;
2) Check whether there are corresponding metal particles in the original data;
3) For bad products, strong magnetic or other metal separators can be used to sort out metal particles;
4) Add a filter for non-reinforced vehicles.
8. Poor plasticization
Seen from the cut surface of the pellets, there are refractory materials, or the appearance of black and toad skin.
The causes of poor plasticization include low heating temperature, impurities in the original material, excessive feeding speed, too weak screw shear, and too much smoothing agent in the formula.
Main treatment measures:
1) Control the temperature according to the process rules, and increase the temperature appropriately when it is found to have poor plasticization;
2) Check whether there are impurities and insoluble matter mixed in the raw materials or in the process;
3) Properly control the feeding speed to increase the time for the plastic to be heated and plasticized in the screw;
4) Choose the screw combination that can cut moderately;
5) Adjust the formula appropriately.
9. Excessive moisture
Look at the shiny water from the surface of the material strip, or feel the pvc material particles damp by hand, or drip water under the pelletizer, and other similar phenomena.
Excessive water content is caused by excessive immersion of the material strips, failure to split the strips in time when driving, the pelletizer speed is too fast, the wind knife wind is too small, and the distance between the pelletizer and the wind knife is too close.
Main treatment measures:
1) Properly adjust the length of the strip soaked in water;
2) When pulling strips, the strips will be divided into strips immediately after entering the pelletizer;
3) Properly adjust the speed of the pelletizer and the height of the whole strip holder;
4) Ensure that the wind knives are strong enough, and use two wind knives when necessary;
5) Properly adjust the interval between the pelletizer and the air knife.
10. Crushed
After the PVC material is cut by the pelletizer, many fine powdery particles are produced. Due to the static electricity of the plastic, the crushed particles will be adsorbed at the bottom of the vibrating screen.
The main reasons for the crushing are excessive immersion of the material strips, the cutters of the pelletizer are worn, too much filler, the material strips are too hard and so on.
Main treatment measures:
1) Properly adjust the immersion amount of the strip;
2) Change to a new cutting tool;
3) Properly adjust the formula to reduce the interval between the pelletizer and the air knife.
11. Carbonization
The leaking material at the die is scorched and turned into a black substance, and the plastic surface appears to be granular scorch.
The main reasons for carbonization are that the heating temperature is too high, forming melt scorch; the screw is used for a long time without cleaning, and the scorch accumulates; the downtime is too long, and the head and screw are not cleaned.
Main treatment measures:
1) Frequently check whether the heating system is normal, and deal with it in time if there is a problem with the heating system;
2) Regularly pump the screw or clear the machine head to completely clear and clean;
3) The screen, filter, and die should be cleared in a timely and clean manner to avoid carbonization. If carbonization is found, the head and screw should be cleared immediately. Clean and avoid carbonization. If carbonization is found, the machine head and screw should be cleaned immediately.
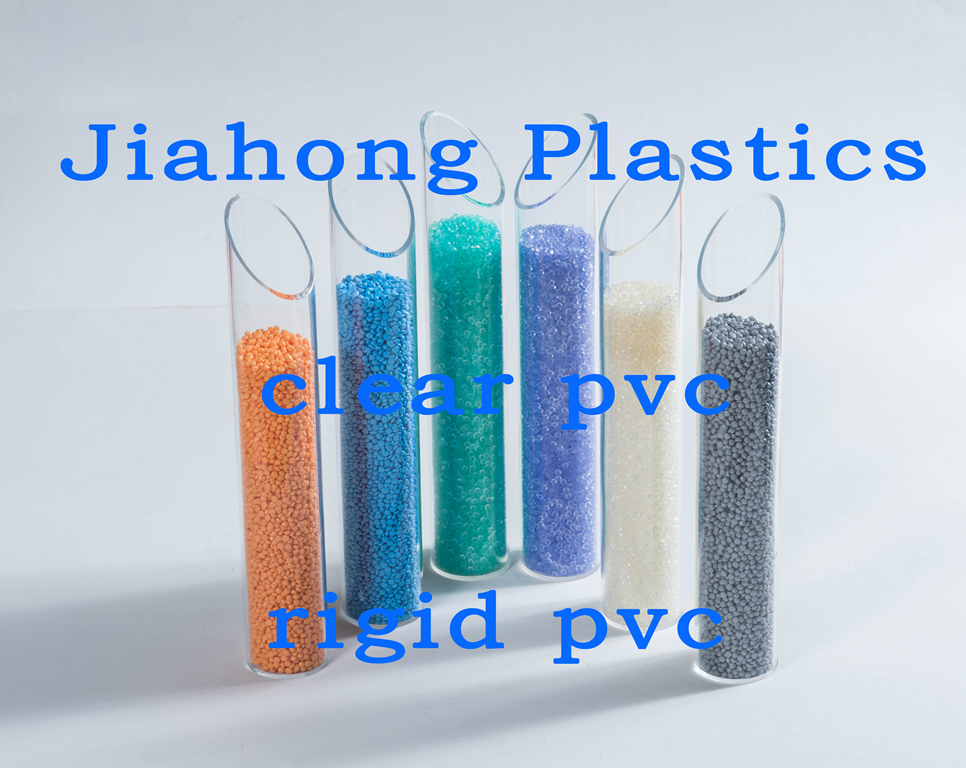
Wuxi Jiahong Plastic Technology Co., Ltd. has nearly 30 years of R&D and production experience in rigid transparentpvc granules, pvc pellet production, and R&D and production experience in modified engineering plastics; a professional technical service team can provide customers with one-stop modification Plastic system solutions. If you want to know more about the product, please log in to our official website: www.js-plastics.com, consult online customer service or call the hotline. Landline: 0510-68755207 Mobile: 15190220696, we will serve you wholeheartedly.
(Disclaimer: All the tutorials and resources included in this site are from the Internet, and their copyright belongs to the original author and his website. Although this site strives to preserve the original copyright information, it may not be able to be determined due to many reasons. The true source, please forgive the original author! If you have any objections to the attribution of the tutorials and resources on this site, please notify the editor immediately. The situation is true and we will delete it as soon as possible.)