一、欠注
成因及对策
1.供料不足。应适当加大供料量。
2.成型周期太短。应适当延长。
3.注射压力偏低。应适当提高。
4.注射速度太慢。应适当加快。
5.原料干燥不良。应对原料进行干燥。
6.料筒或模具温度太低,流道冻结过早。应适当提高料筒或模具温度,扩
大流道截面积,增加注射速度。
7.制品壁太薄。应在可能的情况下适当加厚。
8.浇注系统结构尺寸偏小。应适当放大浇口和流道截面。
9.模具排气不良。应增加模具排气。
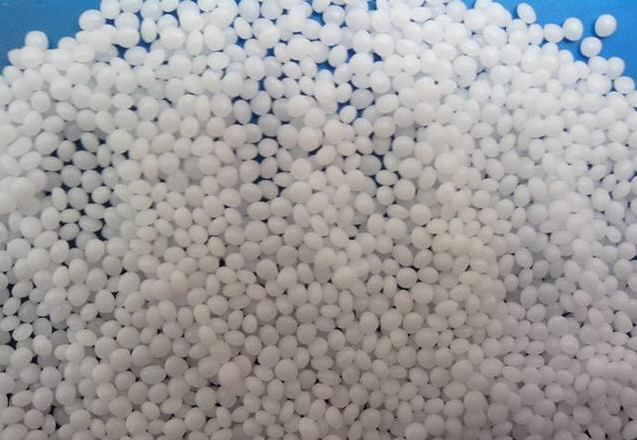
二、溢料飞边
成因及对策
1.熔料温度太高。应适当降低。
2.注射压力太高。应适当降低料筒和喷嘴温度。
3.锁模力不足。应增加锁模力。
三、真空孔
成因及对策
1.成型温度太高。应适当降低。
2.浇口位置设置不当。对于壁厚部位,应重新配置浇口。
3.注射压力偏低。应适当提高。
4.保压不足。应适当延长注射保压时间。
5.注射速度太慢或太快。应根据具体情况适当调整。
6.模具温度太高。应适当降低。
7.射料杆前进时间太短。应适当延长。
8.浇注系统设计不合理。应适当放大浇口和流道截面积。
四、气泡及表面麻点
成因及对策
1.制品冷却收缩的部分不能由保压补料所充分弥补时,就会在制品表面产生小孔或气泡。应适当提高注射压力和延长保压时间。
2.缓冲量不足。应适当增加。
3.喷嘴温度太低。应适当提高。
4.浇口截面尺寸太小。应适当放大。
5.浇口位置设置不当。对于壁厚部位,应重新配置浇口。
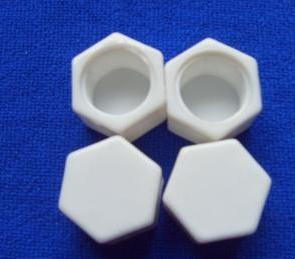
五、缩瘪
成因及对策
1.料筒温度太高。应适当降低成型温度。
2.注射压力偏低。应适当提高。
3.注射速度太快。应适当降低。
4.成型周期太短。应适当延长。
5.保压时间太短。应适当延长。
6.浇注系统结构尺寸偏小。应适当放大浇口和流道截面。
7.浇口位置设置不当。应重新定位浇口。
8.供料不足。应适当增加供料量。
六、空洞及烧焦
成因及对策
1.模具排气不良型腔中的残留空气被熔料包裹,受到绝热压缩,形成空洞,周围的树脂被烧焦。应通过改变浇口位置和增加模具排气来解决。
2.模具偏芯或偏厚。应进行修整。
3.注射速度太快。应适当减慢。
七、熔接痕
成因及对策
1.熔料温度太低。应适当提高喷嘴和料筒温度。
2.注射速度太慢。应适当加快。
3.浇口截面尺寸太小。应适当放大。
4.模具温度太低。应适当提高。
八、波流痕
成因及对策
1.注射压力太高。应适当降低。
2.模具排气不良。应增加模具排气。
3.浇注系统结构尺寸偏小,流动阻力太大。应适当放大浇口和流道截面。
九、霜纹
成因及对策
1.料筒温度太高。应适当降低成型温度。
2.模具温度太低。应适当提高。
3.注射速度太快。应适当减慢。
4.原料中水分含量太高。应进行干燥处理。
十、银丝及斑纹成因及对策
1.成型工艺条件控制不当。应适当调整。
2.滞留物的过热分解导致产生银丝及斑纹。应清除分解的滞留物。
3.料筒或喷嘴局部过热,导致熔料过热分解。应适当降低料筒或喷嘴温度。
4.注射压力和注射速度太低或太高都会产生银丝及斑纹。一般情况下,型腔压力不足容易产生这种故障。对此,应适当提高成型和模具温度,增加熔料的流动性,并适当提高注射压力和延长成型周期。若在型腔压力较高的条件下产生银丝及斑纹时,应适当降低银注射压力和注射速度。
5.喷嘴孔径太小,应换用孔径较大的喷嘴。
6.原料干燥不良。一般情况下,80~90℃条件下干燥3~4小时。
7.浇注系统结构尺寸偏小。应适当放大浇口和流道截面。
十一、冷料瑕痕
成因及对策
1.产生这一故障的主要原因是由于冷料随同熔料进入型腔,导致浇口附近产生疵点。对此应适当提高模具温度,扩大浇口截面,改变浇口位置和降低注射速度。
2.在设计制品的形体结构时,壁厚截面变化太快。应平滑过度。
3.浇注系统设计不当。应修改设计,使熔料充模顺畅。
十二、表面皱纹
成因及对策
1.产生表面皱纹的较主要原因是模具型腔压力不足。应适当提高注射压力。
2.浇注系统结构尺寸太小。应适当加大喷嘴、浇口和流道截面,防止压力损失。
3.模具温度太低。应适当提高。
十三、表面波纹
成因及对策
1.表面波纹和表面皱纹较难区别,所不同点在于波纹是因浇口的喷射现象引起的。因此,应适当扩大浇口截面及减慢注射速度。
2.模具温度太低。应适当提高模具温度,增加充模冷料的流动性能,使浇口喷射产生的波纹不留在制品表面。
3.浇口位置设置不当。应选择即使发生浇口喷射波纹,在外观上也没有很大影响的部位设置浇口,也可采用凸浇口形式。
4.注射机注射量不足也会引起制品产生表面波纹。对此,应换用规格较大的注射机。
十四、边缘处产生弧形
成因及对策
1.熔料温度太低。应适当提高喷嘴和料筒温度。
条纹及麻点
2.注射压力太低。应适当提高注射压力和保压压力。
3.模具温度太慢。应适当提高。
十五、烧焦及变色
成因及对策
1.熔料过热分解或在料筒内滞留时间太长。应适当降低喷嘴及料筒温度,或换用小容量注射机。
2.注射速度太高。应适当降低。
3.加料过程中,树脂粒料带入料筒的空气排不出来。应通过加大背压,从料斗中排气。
4.模具排气不良。应增加模具排气,并适当调整充模速度。
十六、表面污物淀积
成因及对策
1.聚甲醛原料中的添加物污染了模具或微量甲醛气体与模具接触后产生了了水,引起制品表面污物淀积。对此,一是合理控制模具温度、熔料温度、注射速度以及合理设置排气系统;二是保持模具清洁,若模腔表面有大量沉积物粘着,可用竹勺、黄铜勺等不易损伤模具的工具铲刮,也可用专门的MD清洁剂去除。
2.成型工艺条件控制不当是产生淀积物的主要原因。成型聚甲醛时,一是注射速度不能太快,否则模腔内的气体不能及时排出,会引起熔料绝热压缩,促使淀积物产生;二是模具温度必须合理控制,若模温太高或太低都会引起甲醛游离出来形成淀积物;三是熔料温度不能太高,而熔料在料筒中的滞留时间不能太长,否则会使聚甲醛变化或促使甲醛气体游离;四是聚甲醛原料必须充分干燥,因为水分会促使淀积物的产生。
十七、尺寸波动
成因及对策
1.料筒温度的波动引起制品结构尺寸的变化。应稳定料筒温度。
2.缓冲量变化不定引起尺寸波动。应使缓冲量保持恒定。
3.模具温度太低或太高都会导致尺寸波动。应准确控制模温。
4.注射速度太慢。应快速充模。
5.制品冷却不均匀,引起尺寸不稳定。应采用退火工艺处理脱模后的制品,制品脱模后仍需均匀冷却。
6.模具设计不当。对于多腔模具,应合理设计型腔排列形式合浇口尺寸,确保充模同步。
十八、翘曲变形
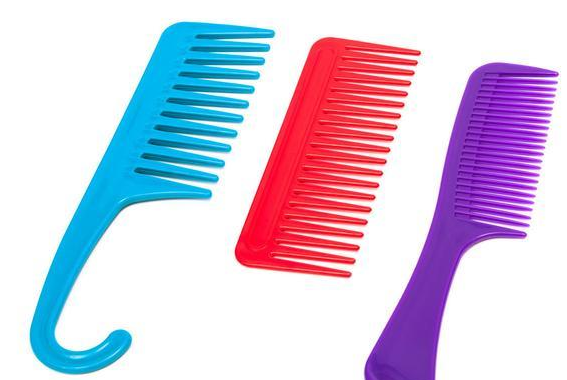
成因及对策
1.模具温度不均匀。模温不均匀会使温度较高部位制品表面收缩较大,因此,应尽量使模温均匀,并适当降低模温,延长冷却时间。应适当提高料筒温度。
2.成型周期偏短。应适当延长。
3.注射压力太低。应适当提高。
4.冷却不均匀或冷却时间太短。制品脱模后可在矫正框中进一步冷却定型。
5.保压时间偏短。应适当延长。成型时,注射时间较好比浇口封闭时间略长为好。
6.浇注系统结构设计不合理,导致充模时熔料流动方向不平行,各部位收缩率差异较大。在选定浇口位置时,应使熔料在模腔内平行流动,浇口形式较好采用多点式点浇口。
7.制品结构设计不合理。在设计制品形体结构时,应尽量减少壁厚差异,避免引起较大的收缩差异。在制品的薄弱部位,可设计一些加强筋,防止收缩变形太大。
8.模具装配不良。分型面未对中。应重新装配模具。
十九、脆弱破损
成因及对策
1.喷嘴部位温度太低。应适当提高喷嘴温度并清除喷嘴滴涎形成的早凝废料。
2.成型周期偏短。应适当延长。
3.注射压力偏低。应适当提高。
4.保压时间太长。应适当缩短。
5.模具排气不良。应增加模具排气。
6.原料干燥不良。应进行预干燥处理,降低原料中的水分和易挥发物含量。
7.喷嘴和主流道间有冷料滞留。应清除冷料,排除喷嘴处的滴漏现象。
8.由于模具温度太低,注射压力过高,以及壁厚不均匀等原因,导致制品内集中了大量的残余应力,引起制品脆化。应调整模具温度、注射压力及保压时间,制品壁厚应尽量均匀,减少加工残余应力。
9.制品的转角处无过渡圆弧,尖角产生应力集中,导致制品脆化破损。在设计制品时,要减少尖角,圆滑过渡;在成型过程中,要防止产生毛刺。
10.熔料过热分解导致制品脆化。应降低过热部位的温度。
11.原料中混入杂质异物,应清除原料中杂质异物,拆卸和清洗螺筒及喷嘴,并检查原料中再生料回用比例是否太高,适当减少其用量。
二十、粘模芯
成因及对策
1.注射压力太高。应适当降低。
2.注射保压时间太长。应适当缩短。
3.模具脱模斜度太小。应适当增加。
4.模具闭合时间太长。应适当缩短。
5.模芯处温度太高。应适当降低。
6.浇口位置不当,应设置在壁厚处。
7.注射机规格太小。应选用较大规格的注射机。
8.垫料太多。应适当减少垫料。
二十一、粘模腔
成因及对策
1.垫料太多。应适当减少垫料。
2.注射压力太高。应适当降低。
3.螺杆转速太低。应适当提高。
4.螺杆前进时间太长。应适当缩短。
5.模具温度太高。应适当降低。
6.注射背压不足。应适当提高。
7.模具闭合太快。应适当延长模具闭合时间。
8.脱模斜度太小。应适当增加。
无锡嘉弘塑料科技有限公司可根据客户要求染色加工ABS、PS、PC、PC/ABS、PP等工程塑料粒子;各种填充、阻燃、增强改性ABS、PP、PC/ABS、PA等工程塑料粒子;各种汽车门板、保险杠、仪表板、发动机盖板、车灯等汽车专用料。
无锡嘉弘塑料科技有限公司拥有近30年PVC粒料的研发、造粒生产经验,改性工程塑料的研发和生产经验;专业技术服务团队可为客户提供一站式改性塑料系统解决方案。如想了解更多关于产品的信息,欢迎登录我们的官网∶www。js-plastics。com,咨询在线客服或拨打热线。固话:0510-68755207 手机:15190220696,我们将竭诚为您服务。
(免责声明: 本站内收录的所有教程与资源均来自于互联网,其版权均归原作者及其网站所有,本站虽力求保存原有的版权信息,但由于诸多原因,可能导致无法确定其真实来源,请原作者原谅!如果您对本站教程与资源的归属存有异议,请立即通知小编,情况属实,我们会尽快予以删除。)